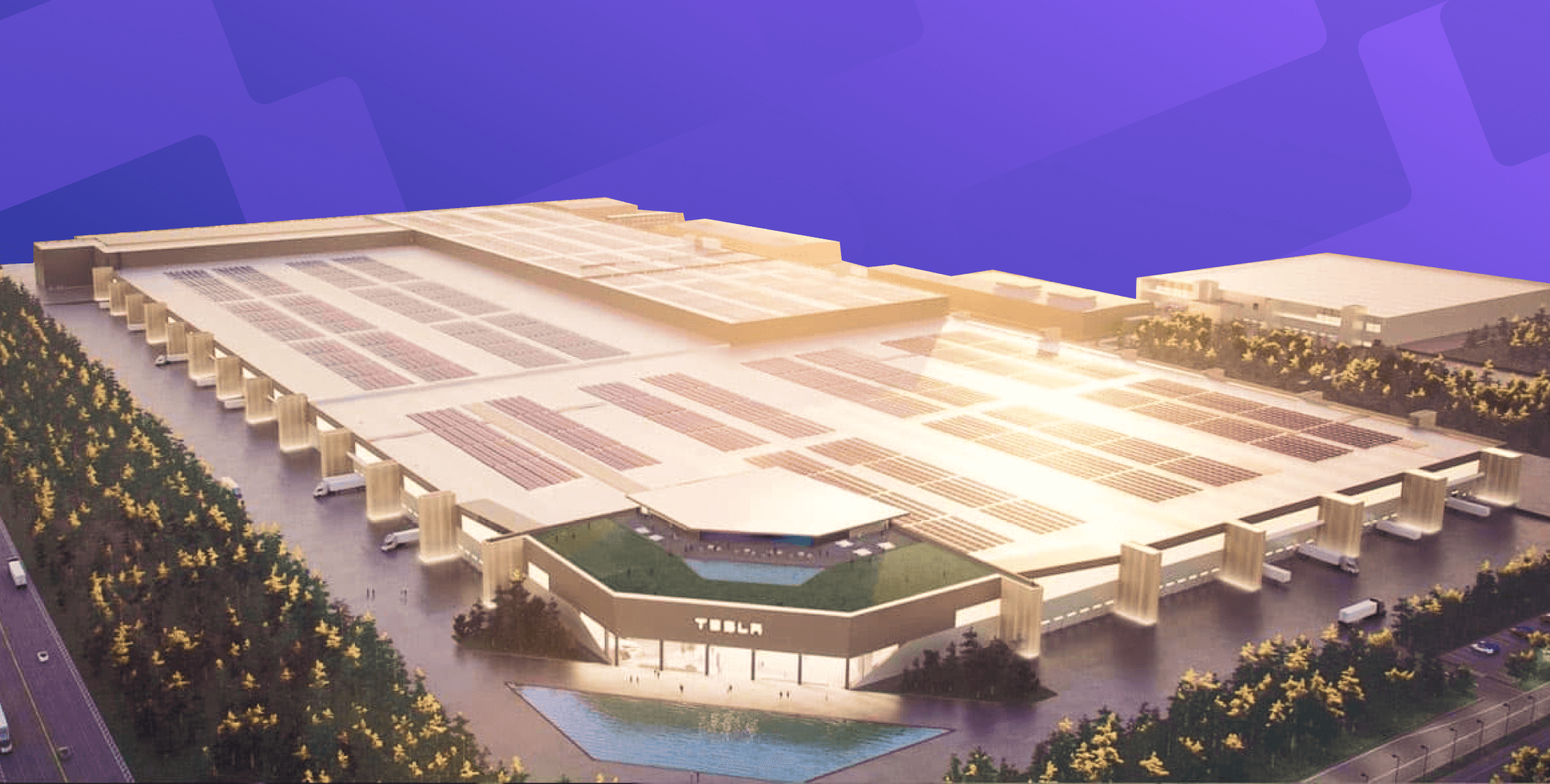
Tesla, a known brand identity today, once struggled to expand its footprint in the automobile industry due to the shortage of skilled labor, adverse weather conditions and the supply chain disruptions that often took place.
These issues didn’t align well with the ambitious, quick turn around factory setup plans of Tesla. Thus the company adopted Prefabrication as an innovative way to build its factories.
The purpose of prefabrication was to shorten the duration of factory construction without any compromises. And at the same time being cost efficient.
Continue reading the blog to understand this smart breakthrough.
Key Challenges Faced by Tesla While Building its Factories
Tesla has primarily been using conventional techniques to build their factories. However, the labor-intensive and time-consuming nature of traditional construction methods has posed various challenges for the automotive company in the past. Mentioned below are some fundamental issues that Tesla has faced during the construction of their factories.
1. Supply of Labor
The availability of skilled labor was a severe concern for Tesla. Since the company wanted to rapidly expand its footprint, it aimed to accelerate its construction processes. However, this is difficult to achieve through physical labor since many intangible factors such as skill and technique come into play when dealing with people.
2. Weather
In 2017, Tesla faced several challenges during the construction of their Gigafactory 2 in New York, due to a harsh winter that brought heavy snow and ice. Unpleasant weather became another roadblock for the company. Heavy rain, snow, or extreme temperatures can slow down any construction work, making it difficult to stick to the project timeline.
3. Supply Chain Disruptions
The COVID-19 pandemic has had a profound impact on construction projects worldwide, including those of Tesla. The supply chain disruptions caused by the pandemic led to delays in the delivery of crucial materials and equipment needed for the construction of their factories.
4. Transportation and Logistics
Construction components need to be transported to the site, which was a logistical challenge for Tesla. The transportation process can be complicated and costly, especially for large and heavy components that require specialized equipment and permits to move.
5. Environmental Concerns
As Tesla strives to build eco-friendly factories, the conventional construction processes have been a roadblock. Traditional methods are time-consuming, expensive, and barely sustainable, which can clash with the company's future-forward ideology.
Why did Tesla turn to Prefabrication?
For the longest time, Tesla has been relying on traditional on-site construction methods to build its factories. This approach often involved the coordination of multiple professional stakeholders, followed by several months of collating and setting up the necessary infrastructure and machinery. However, due to the complexity of the project, there was always a risk of going over budget or delaying construction, or both. To overcome these challenges and speed up production to meet the increasing demands of its products, Tesla turned to prefabrication.
What is Prefabrication?
Prefabrication is a construction technique that involves the production of building components, off-site in a controlled environment, typically a factory. These components are then transported to the construction site for the final assembly.
In modular construction, prefabrication can help produce multiple identical copies of several infrastructural elements in a factory setting. This ensures consistent quality of building components that can be made with similar standards of construction, reducing the likelihood of errors and inconsistency arising during the final assembly.
Read: What is Modular Architecture, Its Advantages, And 10 Examples (2024)
How is Tesla Using Prefabrication to Build its Factories?
Adopting prefabrication for the construction of its factories has allowed Tesla to significantly improve their construction both qualitatively and quantitatively. They use the technique of "advanced framing," to pre-cut and assemble building components in a factory. Everything from the structural framing to electrical, and plumbing systems is factory-assembled before transporting to the construction site.
This modular construction process begins with the design of the building which is then used to create detailed plans and specifications that guide the production of the building components. These components are manufactured using a combination of automated and manual processes, with the help of either computer-controlled cutting machines and robots, or skilled laborers. Once the building components are manufactured, they are then transported to the construction site and assembled using mechanical equipment.
How Tesla Factories are Leveraging Prefabrication?
Prefabrication is enabling Tesla to grow its presence around the world and become a global automobile leader. Its factories are designed to be modular or prototypical, which implies that they can be easily reconfigured as per site conditions.
Below we mention the key advantages of prefabrication that have enabled Tesla to accelerate the construction of its factories.
Time Saving
By using factory-made building components, Tesla has been able to achieve time efficiency. Further, prefabrication has helped them avoid delays due to bad weather conditions and labor issues which are a severe concern in on-site construction projects. For example, Tesla's Gigafactory in Shanghai was built in just 168 working days which is a fraction of the time it would have taken using traditional construction methods.
Quality Control
Prefabrication has allowed Tesla to standardize the quality of building components and ensure that they meet specification requirements. Any issues in the product quality are addressed in the factory before transporting the product on-site. This has resulted in a higher-quality product with fewer issues faced during construction.
Cost Saving
When mass-produced, prefabrication is more economical when compared to traditional methods of construction. In the case of Tesla's Gigafactory in Shanghai, the final cost of construction accounted for a total of $2 billion, which is significantly less than the estimated amount of $5 billion for a factory with a similar footprint, using traditional construction methods.
Enhanced Safety
Prefabrication happens off-site in a controlled environment automatically reducing the amount of on-site construction. This, in turn, helped Tesla reduce site-associated risks, such as falls, slips, trips, and other accidents.
Adaptability
Prefabrication empowered Tesla to experiment and innovate with its factory design. It provided more flexibility to the designers to create more efficient, functional, and aesthetically pleasing building layouts. This adaptability allowed Tesla to quickly respond to new technological advancements and business demands, giving the company a competitive edge in the industry.
Scalability
Prefabrication helps construction projects to be easily scaled up or down. This is particularly useful in the automobile industry, where market demand can fluctuate, and companies need to quickly adjust their production capacity to meet changing needs.
Sustainability
Prefabrication is a construction method that is not only more efficient but also more environmentally friendly. It generates less waste co
mpared to traditional construction methods, resulting in a reduced carbon footprint. Tesla's Gigafactory in Nevada is an excellent example of this, as it produced 83% less waste than a conventional construction project of the same size. Furthermore, Tesla's use of sustainable appliances, such as solar panels and batteries, in their factories, further reduces their environmental impact to a minimum.
In Conclusion
It is exhilarating to see organizations like Tesla advocating for sustainable and modern building practices. By using prefabrication for the construction of its factories, Tesla is aligning with its commitment to reducing the carbon footprint of human activities. This attempt is leading the way forward for automobile companies to achieve their desired economic growth.
Do you wish to learn more about prefabrication? If yes, then check out Master Computational Design Course by Novatr. The course will offer you insights into computational theory and industry workflows.
Explore the course today!
Was this content helpful to you