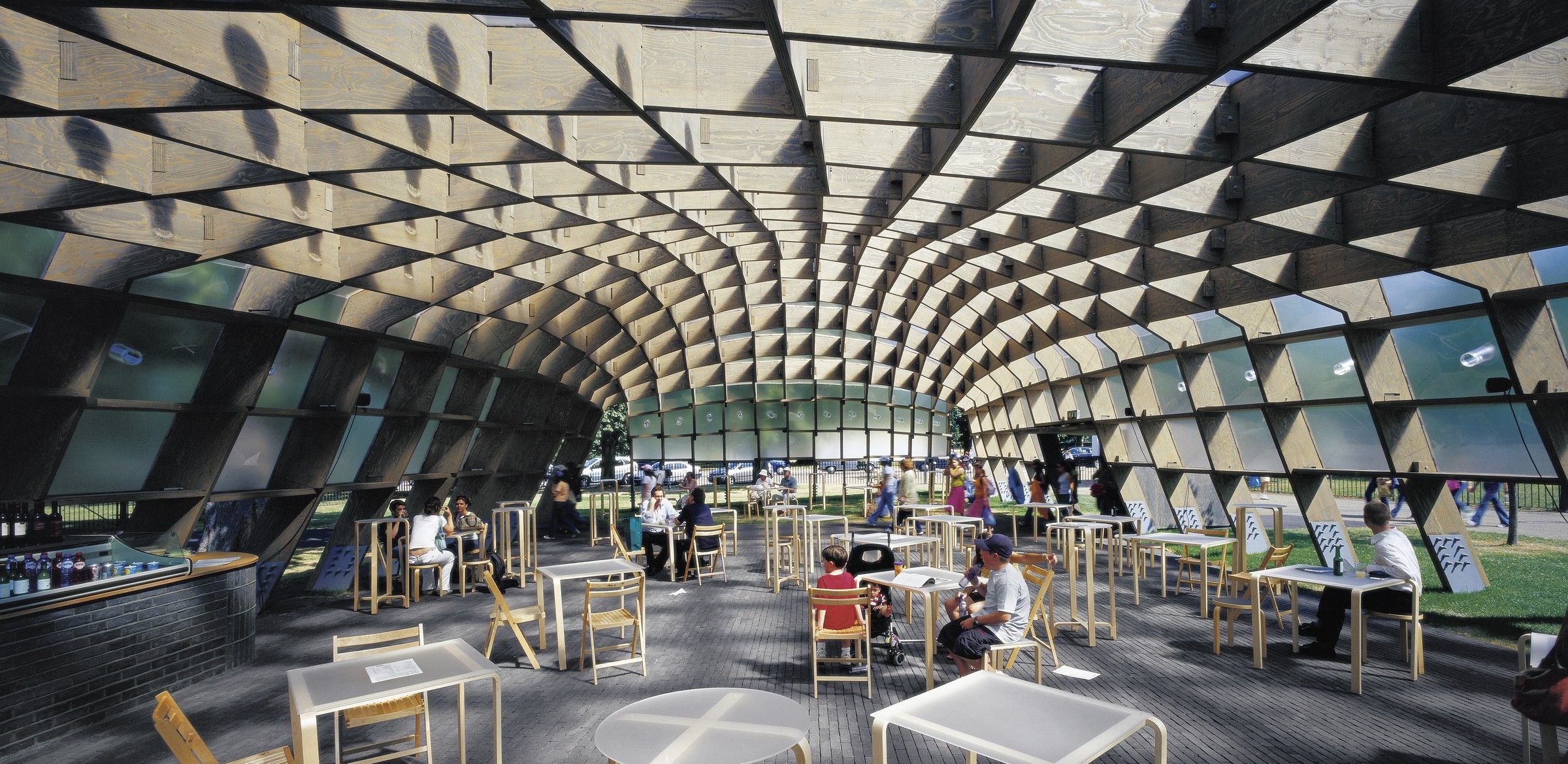
The Serpentine Pavilion is a prestigious annual architectural commission in London's Kensington Gardens that has served as a platform for some of the most prominent architects worldwide to showcase their creative vision. In 2005, the renowned Portuguese architects Alvaro Siza and Eduardo Souto de Moura joined forces to design a remarkable structure for this esteemed project. Their collaboration on the Serpentine Pavilion 2005 merged their unique architectural philosophies and expertise, giving an extraordinary architectural wonder.
The Pavilion showcases simplicity, elegance, and a powerful connection to the surrounding environment. Its clean lines, detailed craftsmanship, and seamless integration with Kensington Gardens' natural landscape make it a temporary haven for visitors to enjoy art, culture, and nature. It also highlights the joint dedication of both architects to outstanding architecture, creative innovation, and the ability of design to form effective bonds between people, nature, and the constructed environment. Their contribution to the Serpentine Gallery Pavilion series left a lasting impact on the architectural realm, inspiring future designers and strengthening their reputation as visionaries.
Serpentine Gallery Pavilion: Design Concept
International architects Alvaro Siza and Eduardo Souto de Moura aimed to create a simple structure that blended with Kensington Gardens' natural beauty, providing visitors with a peaceful and immersive experience. By emphasizing clean lines, minimalism, and tranquility and removing unnecessary ornamentation, they allowed the design’s form to use the play between light and shadows to take center stage.
Serpentine Pavilion 2005 consists of a 300-meter-square enclosure without columns. The roof and walls were made of a continuous grid of wood beams that are offset, wavy, and straight. The top reached its highest point at 5.5 meters above the ground, where the wall stood 3 meters tall. The pavilion was made using 427 distinct types of timber beams that came together in creative grillage patterns to create an organic shape. All wood components are arranged in a mutually supportive arrangement using mortise and tenon joints. A total of 348 translucent poly-to-solar lights illuminate the Pavilion's exterior. The idea was to make things right, blend in with the surroundings, and provide guests with a peaceful, immersive experience. They demonstrated their ability to build places that go beyond simple functionality and offer deep links.
Also Check : How Computational Design Tools Are Easing the Design and Build of World of Volvo
Material study
The architects carefully chose materials that matched their vision and aesthetic, while also considering practical factors like construction and the environment. They used timber beams, polycarbonate panels, and solar-powered lights in the pavilion. The architects selected wood due to its warmth, natural beauty, and ability to blend with the environment.
1. Timber Beams
The Finnish spruce laminate veneers, Kerto S LVL grade Q, measuring 550 x 69 mm, were utilized to make the beams. Compared to other conventional timber products, the material can support more weight. It is regarded as a lightweight substance as well. It possesses the strength, steadiness, and dimensional stability required for long-span structures. The pavilion is made of laminated veneer wood that takes up about 60 cubic meters.
2. Polycarbonate Panels
The Pavilion's exterior cladding features 5-millimeter thick, transparent polycarbonate panels. 348 panels were crafted with unique designs using Computer Numerical Control (CNC) machines based on computer-powered light investigations of computer models created by the Address generation unit (AGU). Its transparency and weather-resistant properties drove the choice to use polycarbonate.
3. Solar Powered Light
An independent solar-powered light is installed in each polycarbonate panel. At nightfall, the light automatically turns on, illuminating the Pavilion's interior and casting an ethereal glow from the outside. The pavilion floats above the ground as the lowest of 1.3 meters are not covered by panels. The solar lights also illuminate one by one, due to the varying orientation of each panel.
Use of digital fabrication
Digital fabrication technologies have opened up new possibilities in the architectural, engineering and construction (AEC) domain, especially since their wide adoption in the 21st Century. These tools have enabled architects and engineers the world over to challenge established procedures and bring innovation to the fore, including expanding newness in design perception and creating novel constructive solutions.
The 427 timber beams had different lengths and angles. To ensure precise production, AGU developed a Visual Basic Script. The script used 36 XYZ coordinates to validate the geometry by comparing it to nearby points. AGU also set guidelines to ensure a perfect fit within the interlocking system. Once they had the accurate geometry, AGU performed structural analysis on each timber beam. They simulated each beam using two 1-D beam components in Oasys GSA software. This analysis assessed the timber grid framework's ability to support the building.
Arup used digital technology to define the shapes of the structures. The structural plans for the pavilion were created by the Arup team. Using Oasys GSA(Structural Designing Software). They conducted a thorough structural analysis to guarantee that the entire system was stable. They shared this information with Finnforest Merk using three-dimensional files and text files with coordinates. Finnforest Merk's CNC programmers verified the data and turned it into CNC instructions in an Excel format. These instructions are used as the basics for the manufacturing process. Since the process relies on the provided coordinates, no 2D-printed drawings are used for fabrication. Finnforest Merk uses robotic manufacturing in Germany to create wood beams. The process involves using compressed Excel-based CNC instructions. They use a 5-axis robotic arm that is fully articulating and linked to the machine.
Manufacturing
Fabricated LVL timbers, an engineered wood product, are transported from Finnforest Merk's factory to a London construction site. These timbers are efficiently packaged and loaded onto trucks, taking only two lorry loads. Finnforest Merk manages the construction management process, supervising on-site assembly and installation. The installation of timber beams takes about one month, and only ten joiners are involved in the construction process. Prefabricated LVL timbers require fewer workers compared to traditional methods, making the construction process more efficient.
Proper labeling is crucial during the delivery process, with each wood labeled with a unique structural grid reference. This system enables on-site workers to quickly identify the location of each timber, which is essential for the erection sequence during construction. The use of prefabricated LVL timbers in construction projects allows for efficient transportation, fewer labor requirements, quicker construction time, and accurate placement of timbers using a labeling system.
Mounting and Demounting Process
The Pavilion's interlocking structure required a well-thought-out erection sequence to be defined. The erection process started from one corner and radiated to the opposite corner. Each new piece of timber beam was slotted into places that were already in place. The Serpentine Gallery had requested a pavilion that would be purposefully constructed as a demountable structure that could be sold when the exhibition was finished since the project's inception. In response to that demand, Siza and Souto de Moura solely used mortise and tenon joints for the timber grid structure's interlocking system—no fixed connections were used. This connection technique allowed for quick assembly and disassembly of the Pavilion. The building's structure is designed to fit together like a 3D jigsaw puzzle, thus the demountable procedure had to be carried out in the right order to prevent an early collapse.
In Conclusion
Architecture must collaborate with other experts from various fields because it is not a standalone profession. We could witness how effective communication between the architects and engineers produced a spectacular structure at the Serpentine Pavilion in 2005. Also, in this Pavilion, modern computational and fabrication technology could affect how the structure is created. Without utilizing macro weaving techniques, robot manufacture, or script description for the geometry, The Pavilion would only exist as an abstract idea. These modern methods exist to make it easier for architects to achieve their goals.
Novatr offers a Masters Computational design course where you can enhance your architectural career with a focus in Parametric Design, Generative Design, BIM, and Sustainability in creating such a parametric structure using new tools and technology. Visit our Resources Page for more such interesting blogs
Was this content helpful to you