Simplest Topology Optimisation Guide: Applications, Advantages, & Software | 2025 (Updated)
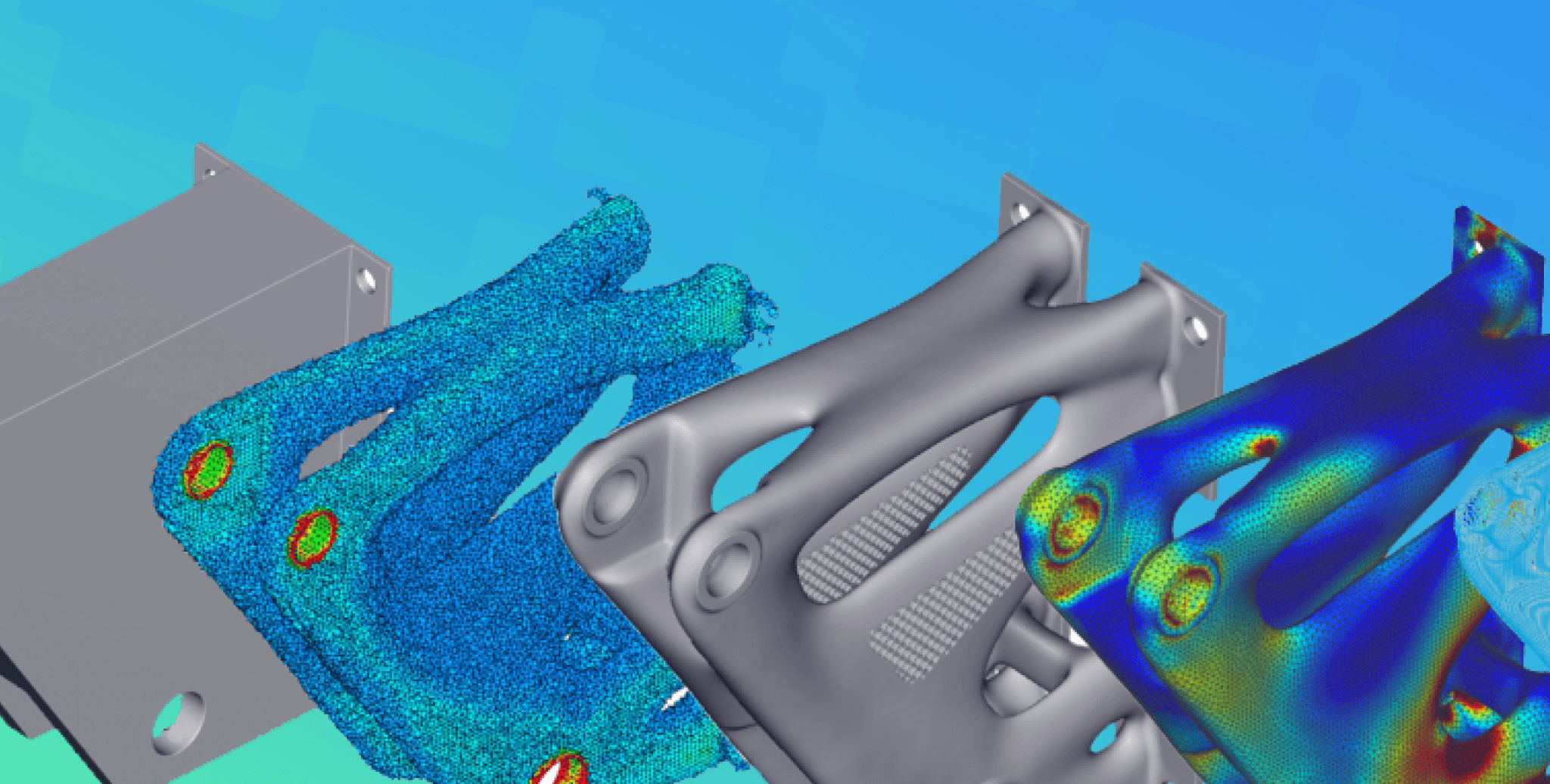
Table of Contents
The advances in technology during the past decade have brought about countless exciting tools and workflows to the AEC industry. Topology optimisation is one such technology that is gaining a small momentum in the industry, riding the coattails of computational design. It is a complex algorithmic process that uses the basis of computational design. But fret not; in this guide, we will explain what the topology optimization process is, its application in the industry, and its tools.
What Is Topology Optimisation?
Topology optimisation makes use of a computational mathematical approach to spatially optimise material layout based on a predefined set of space, loads and other conditions. The layout is a result of performance targets met through this process.
It is an approach used in both architecture and engineering industries, though it is more common in the latter. Nonetheless, some consider topology optimisation an amalgamation of architectural design approaches with engineering principles.
Topology optimisation, along with generative design and form-finding, has brought about new and unique forms into architectural design.
How Does Topology Optimisation Work?
The goal of topology optimisation is to maximise the performance of the given 3D design. Many factors are involved in optimisation:
- Load conditions
- Material & their properties
- Spatial boundary
- Constraints
The process usually happens near the end of the design phase. At this stage, the basic form is complete. Only then, the analysis for optimisation can take place to create an output that is lighter in weight and material usage.
It utilises Finite Element Methods (FEM), or more specifically, Finite Element Analysis (FEA) to analyse and optimise the model. The designer must first define and establish the design space, material properties, external loads and boundary conditions. Defining the design space is important; through FEA, the minimum design space is determined without compromising the strength and functionality of the design.
The topology optimisation tool will then create a mesh which will also be evaluated using FEA to find the optimum load. The process does not end here. The next step is to digitally put pressure on the model to test the structural integrity, stiffness, deflation and stress. Once the analysis is complete, any redundant material will be removed and FEA will export each piece to create the final design.
Algorithmic Generative Design vs Topology Optimisation
Topology optimisation and generative design are not the same. The only similarity is that both make use of algorithms to generate output.
Generative design is the process of using algorithms to generate design. We can use generative design from the beginning of the design process to create a design model. The model, or the form, can still be optimised. Using constraints and algorithms, generative design tools can create multiple designs for architects and engineers to choose from.
On the other hand, topology optimisation comes into play at a later stage. It requires a design model. With generative design, topology optimisation analyses this initial model based on the factors above. This is the FEA process which will analyse, optimise and remove any redundant materials.
Generative design is one of the verticals of computational design.
Read more: Top 6 Verticals of Computational Design Every Architect Must Know.
Application Of Topology Optimisation in Various Industries
Topology optimisation is a useful technique for complex design and engineering solutions. It is best suited for:
- Light-weighting (improving strength-to-weight ratio by removing excess material)
- Shape Optimisation (creating geometry based on specific constraints)
- Structural compliance (calculating forces and the shape’s response to them)
- Multiphysics design (incorporating multiple physical phenomena for optimal design)
Mechanical And Civil Engineering
Topology optimisation has been predominantly used in the engineering sector to design components that maintain their mechanical strength while minimising the amount of material used.
It helps generate engineering product design and is usually used in the design stage. At this stage, it is the most effective and efficient to optimise the form based on material-to-safety and stiffness-to-weight ratios. Structural topology optimisation is a task for architects and engineers to determine the optimised structural design.
Aerospace And Automobile
If there are any industries best suited for topology optimisation, they would be the aerospace and automobile industries. In both industries, mechanical components are central to the entire design where they need to be lightweight and yet have good strength and power. Through the form and materials, it is also possible to optimise the design for lower fuel consumption.
And of course, needless to say, the forms that topology optimisation tools can produce make it an exciting process for new vehicular designs.
Read more: 10 design and engineering fields using computational design besides architecture.
Topology Optimisation And Manufacturing
The role of topology optimisation does not just end in the design phase. Architects and engineers can manufacture the optimised design output using additive manufacturing methods. As a product of advanced computational optimisation, designs generated using topology optimisation can be rather difficult to manufacture using conventional methods. With 3D printing, any shape of any complexity can be produced without wasting resources in large amounts.
Advantages of Topology Optimisation
Design Optimisation
This is a rather obvious fact but it is the major advantage that also brings smaller added benefits to the design. An optimised design balances every quality as a product of the best solution (the best here meaning the most efficient or appropriate). It is made to have a smaller size and weight without sacrificing the structural or component quality.
Fast Process
Topology optimisation is a computational process. The computational algorithms ensure a fast and efficient process by automating certain workflows. The user has to input the right constraints and algorithms, and then just wait for the software program to share the results.
Minimised Material Use
As mentioned before, the output design via topology optimisation is a product that has a smaller size and weight. Any unnecessary material in the design space is removed after a thorough analysis.
Cost
A smaller design means less material used which indirectly renders the product to be cost-effective. We can produce more products with the same amount of materials and resources. What’s more, each individual product will require less energy consumption.
Sustainable Production
Conventional design and production have high energy consumption, even more so to manufacture large products. By reducing the size, the energy consumption for each item is also lowered. The raw materials needed for manufacturing also become minimal. Digital fabrication also ensures a precise design production without any wastage.
Read more: Exploring the Most Innovative BIM Projects in Europe {2024}
Disadvantages Of Topology Optimisation
Limitation In Manufacturing
An asset of topology optimisation is that it can create optimised designs for each project. However, on the other side, conventional manufacturing may be insufficient for each unique production. Products of topology optimisation are best manufactured using digital fabrication methods such as 3D printing, which may not be available for everyone.
Challenges in Implementation
Topology optimisation has only become more significant in the industry in the past few years, due to the rising interest in computational design workflows. Many architects and engineers are still not familiar with computational design. They would need to first understand computational workflows to use topology optimisation in their workflows, which could deter them from adopting the process.
Unintentional Cost and Wastage
Topology model optimisation, or any computational workflow, makes the design exploration stage easier. This can encourage architects and engineers to spend unnecessary long hours or create bulky designs in the name of creativity. Any extra material or resources can incur extra costs and time, as well as a chance for unnecessary wastage.
Topology Optimisation Software
While most users can use computational design tools such as Grasshopper with Rhino 3D with plugins for topology optimisation functions, there are specific topology optimisation software packages that come with built-in optimisation and simulation functions.
Solidworks
In the niche of topology optimisation, Solidworks by Dassault Systemes is a well-known software for design and manufacture. It can cater to various industries, including architecture, aerospace, infrastructure, industrial equipment, marine and transportation.
The simulation solutions provided by Solidworks for topology model optimisation can be utilised for structural analysis, computational fluid dynamics, electromagnetics solutions and injection moulding simulation. The software comes with integrated analysis tools for every architect, designer, engineer and analyst.
Autodesk Fusion 360
Autodesk Fusion 360 for topology optimisation is a great tool for industrial designers, engineers and machinists that works as a cloud-based tool for 3D CAD (computer-aided design), CAM (computer-aided manufacturing), CAE (computer-aided engineering) and PCB (printed circuit board).
It supports -
- 3D modelling
- manufacturing including additive manufacturing
- generative design
- simulation
- data management and collaboration workflows
Creo
Creo is a 3D CAD software by PTC for product innovation. It supports generative design, augmented reality (AR), simulations, additive manufacturing and IoT for better-quality products with faster workflows. With the generative design capability of Creo, topology optimisation connects digital design to engineering, and then to manufacturing.
Creo comes with the Generative Topology Optimisation extension that allows users to optimise the design for manufacturing based on different constraints. It is not just a modelling tool; it also takes a step further into simulation-driven design through Ansys Powered Simulation in Creo. The process enables analyses in real-time for structural, modal, thermal and fluid flows.
Topology Optimisation Plugins For Grasshopper
TopOpt
A plugin for Grasshopper and a research platform, TopOpt provides implementation of architectural and structural topology optimisation. It was developed by the joint effort of the Technical University of Denmark, the Israel Institute of Technology and the Aarhus School of Architecture to extend design methods through optimisation methodologies.
Ameba
Ameba uses the Rhino-Grasshopper platform for parametric modelling and topology optimisation based on Bi-directional Evolutionary Structural Optimisation (BESO) technology. Different loading and boundary conditions are applied to the initial design which will change into different shapes, just like the amoeba organism.
While it still hasn’t achieved much popularity in the architecture industry, topology optimisation is becoming a much-needed process in the engineering and manufacturing industries. Many industry professionals are still getting themselves acquainted with the new emerging technologies to supplement their design workflows. Topology optimisation might just be the new technology architects and engineers should pay attention to.
Learn how to Master Computational Design with Novatr for real-world applications and take advantage of computational power for your design workflows. Taught by industry experts from coveted AEC firms, the focus of the course is on learning how to apply computational design principles to real-world projects.
Want to learn more about computational design? Head to our Resources for more informative guides.